|
Beijing, China. ABB’s Low Voltage Products division, a business of the leading power and automatio
more
Russia’s Far East occupies one-third of the country’s territory and accounts for more than nine
more
A new international development bank and multi-billion emergency lending pool are set to be launched
more
The Nissan in Russia broke the mark of 1 million vehicles (including light commercial vehicles) for
more
Rolls Royce the luxury motor car manufacture just announced a sales increase in the leading Bric cou
more
|
"Companies need to focus their Export
strategy on Growth markets having a plan for the Bric's is vital"
You are here » Home Page
» Industry Sectors
» Rosler Metal Finishng USA, LLC
Rosler Metal Finishng USA, LLC
|
|
Press Releases |
A new dimension for shot blasting of small parts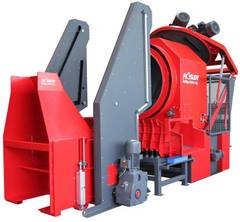 With its intelligent design details and proven components, the innovative Rösler Multi Tumbler ensures high levels of process safety for the shot blasting of mass produced small parts.
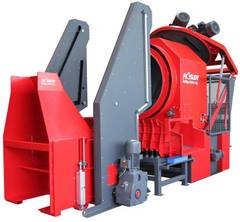 With its intelligent design details and proven components, the innovative Rösler Multi Tumbler ensures high levels of process safety for the shot blasting of mass produced small parts.
Regardless of how parts are produced, be it by casting, forging or stamping, their treatment in batches poses special technical challenges for a shot blast machine. The most important requirement for batch processing is the prevention of the parts getting lodged or damaged during the shot blast process. Of equal importance is the intensive yet gentle mixing of the parts to achieve optimum process results in short cycle times. The new Rösler Multi Tumblers fulfills all these requirements in a spectacular manner!
The unique design produce superior shot blast results A key feature of the Multi Tumbler (RMT) concept is the innovative geometry of the rotary tumbling barrel. The inside of the barrel wall features specially contoured ridges, while the bottom is shaped in the form of a three-sided pyramid. Apart from the fact that the barrel has no gaps whatsoever, this design produces the special “multi tumbling” effect: The ridges in the barrel wall cause the parts to tumble and mix, while the pyramid in the barrel bottom forces the parts to the top of the mass for good exposure to the blast media. This design guarantees the problem-free shot blasting of extremely flat and small parts without any lodging or damage to the parts. During the shot blast process the barrel is sealed closed with a lid preventing any blast media spilling to the outside. The optimum placement of the blast turbine on the barrel lid ensures the complete coverage of the parts batch by the blast stream for absolutely homogeneous and repeatable blast results. The raw parts are placed into the tumbling barrel with a hydraulic loader that tilts by 160° for complete unloading of the parts from the transport bin.
Versatile Multi Tumbler The compact RMT machines are available in different versions and sizes and do not require a foundation pit. Parts with sizes as small as 2.5 mm can be easily processed in this machine type. RMT machines are also suitable for batch processing of large work pieces with sizes up to 600 mm. This is especially advantageous for work pieces with complex shapes and inner contours where spinner hanger or wire mesh belt machines might not reach all surface areas. Depending on the machine size and the processing objectives like general blast cleaning, de-sanding, sand core removal, deburring, paint preparation, up to shot peening and decorative blasting, the Multi Tumblers can be equipped with either one or two turbines. Of course, Multi Tumblers can also be supplied with compressed air blast systems. The RMT machines are available as stand-alone systems. They can also be fully automated and integrated into existing manufacturing lines.
Robust design and easy maintenance The tumbling barrel is made from wear resistant manganese steel. The innovative machine design requires a minimum of wear parts which are easily and quickly replaced. For this reason the multi tumbler from Rösler not only offers superior technical performance for batch processing of difficult parts, it also features excellent wear protection resulting in improved uptime and offering ease of maintenance.
2013-04-22
| Efficient deburring and deflashing of castingsNo other industry has higher quality standards for cast parts than the automotive industry. However, shorter product life cycles, a broadening product range and increasing cost pressures require that manufacturing systems be both extremely flexible and cost-effective. This not only applies to the casting process itself but also to the subsequent deburring and surface finishing steps. In recognition of this fact - and especially in an effort to improve its competitiveness - Koenig Precision Co. recently purchased a new shot blast system for castings.
Efficient deburring and deflashing of castings Tailormade, automated surface finishing solutions
No other industry has higher quality standards for cast parts than the automotive industry. However, shorter product life cycles, a broadening product range and increasing cost pressures require that manufacturing systems be both extremely flexible and cost-effective. This not only applies to the casting process itself but also to the subsequent deburring and surface finishing steps. In recognition of this fact - and especially in an effort to improve its competitiveness - Koenig Precision Co. recently purchased a new shot blast system for castings.
Higher quality and efficiency - with 8 blast wheels Koenig Precision Co. is a specialised job shop for finishing of castings. The business started in 2000 with degating, manual deburring and quality control. Since mid 2006 Koenig has been operating a high production shot blast system. This investment has become necessary for an automotive customer who awarded Koenig their business for deburring and surface finishing of aluminum diecast torque converter and transmission housings. Prior to this significant investment the Koenig management team consisting of Rolf Koenig and Harald Zeiler researched the available blast systems at Rösler and other well known equipment manufacturers in Germany and Europe. Mr. Koenig says, "At Rösler we received extensive technical advice, and they provide us with excellent technical support."
Blast cycle times of 12 seconds The job is not easy: It requires the all-round blast cleaning of a total of 9 different aluminum diecastings weighing from 5,000 to 8,500 grams and a height of up to 400 mm. All parts are "cup-shaped" posing the danger of extensive media carry-out. The infeed cycle time is 12 seconds per part. Rösler developed the optimum blast process for these parts through extensive trials in the Rösler demonstration lab. The result was a RDGE wire mesh belt machine, equipped with 8 high performance Hurricane blast wheels which guarantee an excellent and consistent finish of the complex diecastings. Mr. Zeiler explains that "the special angle at which the blast wheels are mounted ensures that all parts contours and cavities are blasted with the same intensity preventing any "shadowing". The blast results are excellent!"
Dual tracks guarantee high efficiency and quality A special feature of the RDGE 1000-8 is the fact that the wire mesh belt, with a total width of 1000 mm, is divided into two tracks. Currently Koenig is processing 2,500 parts a day. This represents a capacity utilization of less than 50%, offering the company plenty of spare capacity for future growth. To improve its competitiveness the company already replaced manual deburring with deburing robots. Mr. Koenig explains that in a further step "the loading of the shot blast machine will also be automated". Another special feature is the unload system of the shot blast machine: It allows the automatic and consistent removal of all blast media that might be carried out with the "cup-shaped" parts. The reclaimed blast media is automatically returned to the blast machine.
2007-10-19
|
|
BricPartner the Business Partner
search experts for the Bric region
|
Featured Partners
Featured
Developing
Business In Brazil Russia India China and South Africa
|
|